PAS 8700 specifies requirements for Design for Manufacture and Assembly (DfMA) and MMC in new build residential properties (excluding industrial and commercial buildings, hostels, care homes, hotels, prisons and hospitals).
British Standards Institute published the final PAS 8700 (the PAS) on 30 April 2025.
PAS 8700 sets out the process for the effective deployment of MMC; aiming for the improvement of stakeholder understanding and realising the benefits of MMC. As the construction sector has significantly evolved, there is a need for greater consistency in order to increase the use of MMC. Consequently, PAS 8700 has been developed by Ministry of Housing, Communities and Local Government (MHCLG) to provide a single specification which aims to act as a coordinating document that directs its users to other technical requirements. In totality, PAS 8700 aims to support the procurement, design, manufacture, construction and use of safe, resilient and repairable residential buildings that use MMC.
The PAS covers pre-manufactured off-site construction forms of MMC, including the pre-manufacturing of entire buildings, consolidated systems, assemblies, components and elements. Whilst there is reference to the PAS being applicable to categories 1 to 5 of the MMC definition framework, the PAS is not intended to cover traditional building product led site labour reductions or productivity improvement; nor site process led site labour reductions, productivity or assurance improvements.
The PAS specifies the requirements for individual elements and build types for the entire life cycle of a project, including disassembly and recycling, providing a standardised blueprint for both permanent and demountable MMC projects. Whilst much of the PAS is technical in nature, it does contain useful insights into the interplay of contractual considerations and procurement within the MMC sphere.
There is an understanding throughout the PAS that the technical specification provided has been introduced with the backdrop of the fundamental building safety reform in the UK, including the Building Safety Act 2022, the Fire Safety Act 2021 and their associated regulations.
What is MMC and DfMA?
MMC covers any building methods which are designed to improve productivity and safety, while reducing the need for labour. It is a term that is often used to describe off-site production of buildings (as this is a departure from traditional building methods, aimed at improving productivity and reducing labour requirements) but it encompasses any building method with the explicit objective of improving efficiency.
DfMA is a term that addresses two design considerations: (i) how a component is manufactured; and (ii) how it is assembled. The latter is more complex than it may first seem, as the assembly of a component can be bespoke to varying degrees.
PAS 8700 and Implications for Contracts
Insurance, warranties and third-party requirements
The PAS recognises that the assistance of funders, system accreditation bodies and insurance and warranties providers can be utilised to address and identify any requirements to: meet the future insurability of MMC homes (which has long been a worry, given insurers reluctancy to insure MMC developments due to the latent defect risk); the likelihood of and the reasons that mortgage lenders might limit access to lending (as traditional lenders are often apprehensive regarding MMC); and, the perceived risks that could influence the future valuation of a home.
In addition to latent defects insurance, the PAS recommends early engagement with building insurers to establish cover for particular manufactured systems. This is particularly important, as MMC systems often have no historical data to support performance, projections or confirm actual loss experience and this can often limit the market availability of cover.
In respect of contractual considerations, it is important that the manufacturer is obliged to take out latent defects insurance as early as possible as warranty providers will likely need to conduct full technical reviews of the design engineering, manufacturing, transportation, assembly and testing of the MMC system, as well as an assessment of the site, ground conditions, foundation design and construction. It is also important to note that at this early stage of the MMC process, access will need to be granted to the site, and collaboration between the Client and manufacturer is essential in obtaining insurance due to the interplay between system production and installation.
Design
The PAS recommends that a risk register should be created from the outset (or at RIBA stage 0 if used) and this shall form part of the early project management process. Risks should be categorised according to their likelihood, impact and severity. The risk assessment needs to clearly identify those responsible, accountable, consulted and informed (RACI) and have mitigating actions identified. It is recommended the risk assessment is reviewed at each key stage of the project, and confirmation should be sought that the delivery team understands those risks that still require attention and those that have been mitigated. The risk assessment should be maintained until manufacturing, construction and commissioning are completed, and a contractual clarity over the timing of these assessment, the conducting of these assessments and the necessary actions arising from these assessments, is pivotal.
As the PAS recommends that responsibility for design information and information release shall all be agreed at RIBA Stage 1, and that all team members, including the Client, shall agree the point at which design elements are to be fixed (a design freeze), Clients must appoint designers and manufacturers at a much earlier stage than in the traditional design and planning process, and use forms of contract which support early supplier involvement (ESI) as recommended by the Construction Playbook, such as PPC 2000 and pre construction services agreements (PCSA's).
As mentioned below, this design freeze stage must take place before Gateway 2 under the Building (Higher-Risk Buildings Procedures) (England) Regulations 2023 (the Gateway Regulations).
The PAS sets out a matrix of design responsibility across the professional team and recommends services specific to an MMC project for structural and fire engineers.
Whilst early design is important, there is also emphasis placed on the need for the design to allow flexibility and competition in the choice of MMC system. The MMC advisor, a new role recommended in the PAS, has the responsibility to liaise with system manufacturers during the concept design to determine the availability and compatibility of their MMC systems.
Importantly, the PAS also emphasises the need for standardisation and the opportunities it presents for efficiency gains, economies of scale and reducing material waste. The PAS advises designers to identify the benefits and document opportunities to standardise designs, layouts, components and interfaces as far as is practicable to improve quality, safety, maintainability, performance, accessibility and reduce the environmental impact.
Fire and building safety were reflected throughout the draft PAS although no reference was made to co-ordinating with the Gateway stages under the Gateway Regulations. In the final PAS, more thought has been given to the interaction between standardisation and the Gateway stages, with the aforementioned design freezes suggested as being dual purpose to also meet the submission requirements for legislative compliance. Gateway 2 for HRBs in England creates a statutory design freeze and significant procedures for any design changes that are needed after approval of the design application at Gateway 2 and therefore, the design freeze implementation into MMC contracts as standard, assists with adhering to statutory necessity earlier in the process. However, there is still a missed opportunity for further interlinkage between the standardisation of MMC and the Gateway Regulations.
Funding
The PAS recognises that with MMC manufacturing processes, significant financial investment is required at the early stages of the project, for example to enable raw materials to be obtained prior to factory production commencing. The PAS recognises the balance between funders and Clients who will want to mitigate their exposure and limit or impose conditions on advance payments and deposited funds, and the manufacturers who will seek guaranteed cash flow. While large, advanced payments do present exposure for the Client (especially given the vulnerability of many manufacturers within the MMC sphere), protection can be sought from escrow accounts, insurance bonds, letters of credit or advanced payment guarantees, and use of Project Bank Accounts as recommended by the Construction Playbook should be considered.
Quality
The PAS recommends that it should be the role of the MMC structural engineer to agree the codes and standards to undertake the project design works. The PAS does recognise that, for off-site manufacture, there is a need for both factory quality assurance, inspection and testing and on-site testing and commissioning.
The PAS also draws attention to the need for a robust quality assurance process to protect modules and elements during construction and confirm that their fire protection is maintained.
Throughout the project there shall be documented evidence of an auditable system of quality management and assurance in place to govern the manufacture and production of systems, assemblies and components.
There are useful flow charts referencing the key handover points and construction interfaces and the PAS refers to the role of the latent defect insurers inspection team to test quality at key stages.
PAS 8700 and Procurement
The PAS suggests a different approach from tradition projects, as is unsurprising, and recommends that the delivery team is engaged from the outset. This provides an optimised process by relying on the correct approach to client project management, from setting initial client requirements, integrating the team with the appropriate procurement mechanism, and front-loading key decision-making in the pursuit avoiding unnecessary Client change.
The PAS envisions that the Client shall engage designers and other team members, including potential supply chain partners, to align with both strategic objectives and value-based decisions, all with the assistance of the MMC advisor, whose scope should extend into procurement and advanced payment mechanisms, bonds and vesting processes, and advise on the need for and help in defining the roles of other collaborators. The Client will also define designers and other team members scope and responsibilities, to align with the project programme requirements for the manufactured elements. The PAS dictates that the members of the project team shall have experience and knowledge of MMC and DfMA that is appropriate for the scope and complexity of the project or programme.
However, aside from a mention in the checklist triggering Clients to remember that they will need to run a compliant and robust procurement process, there is no guidance on procurement routes or evaluation and selection criteria for manufacturers and professional team members.
Contracts
There is a missed opportunity in the PAS to refer to forms of contract which would be suitable to engage design team members and manufacturers early and to develop design and manufacturing specification and process collaboratively. There is a recognition that MMC hinges upon collaboration and that having the time and opportunity to resolve and coordinate with various design inputs early, in contrast to traditional building projects, is a key tenant of MMC projects, but the PAS stops short of recommended the contractual vehicle. The Construction Playbook refers to using standard forms to reduce negotiation and therefore a form such as PPC 2000 which provides for a pre-construction/ manufacturing period, early engagement, multi-party alliancing relationships and use of project bank accounts would seem an obvious choice and would support the recommendations of the Government's Collaborative Procurement Guidance for Design and Construction to Support Building Safety.
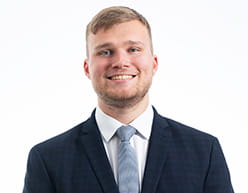